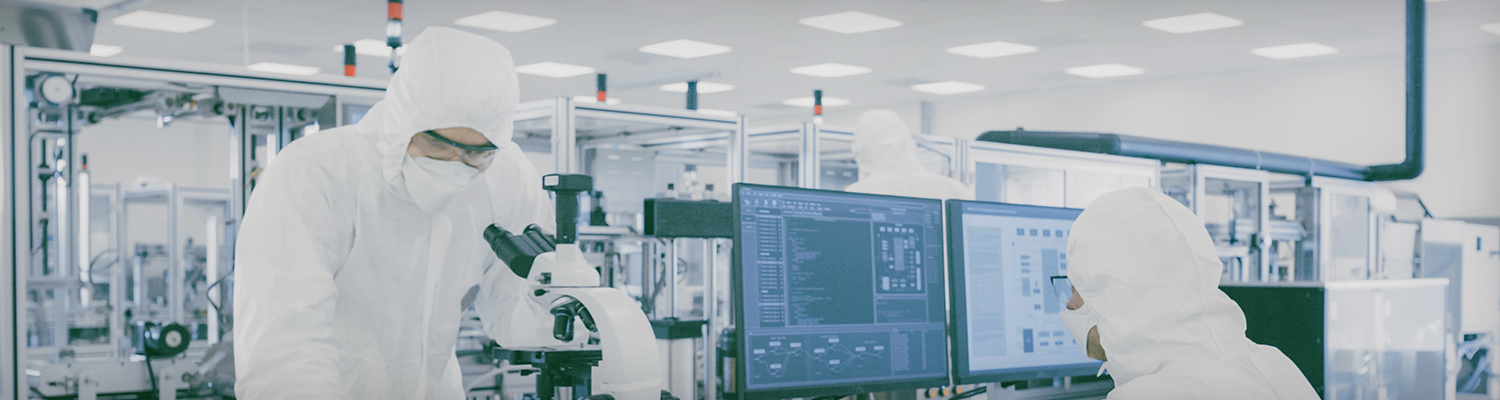
SINJIN PLASTICS
INNOVATION
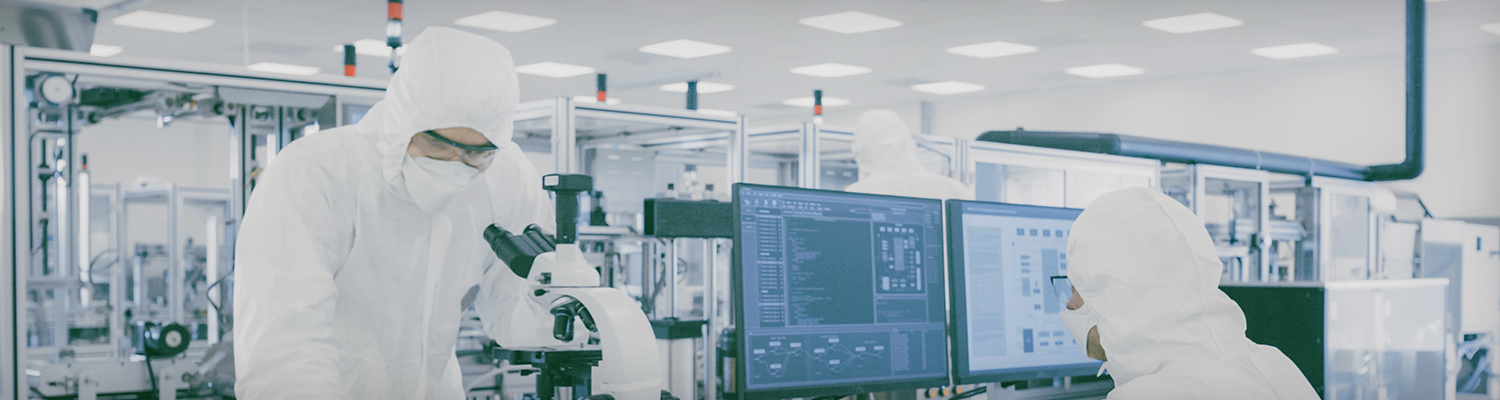
Quality Assurance Organization
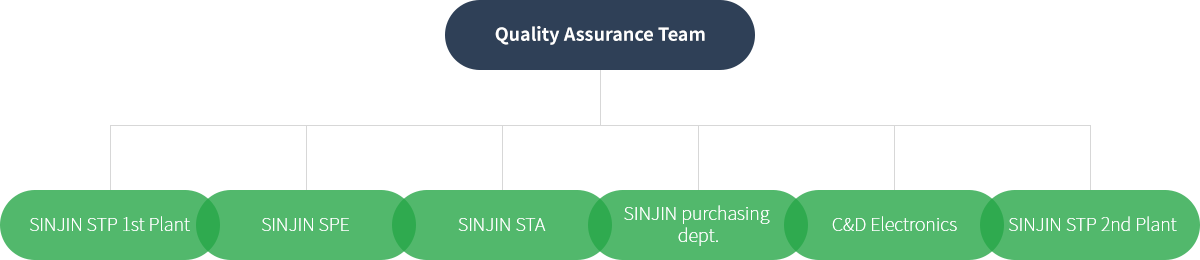
Quality Management Goals
-
Management headed toward the world -
Management of change,
communication, and harmony -
Management based on
technological quality

Quality Principles
-
Compliance with quality assurance process
-
Global quality system adoption
-
Customer trust through quality satisfaction

Quality Goals
-
Quality
Enhancement -
Continuous Improvement
-
Customer Trust
-
Claim Reduction
Warranty System
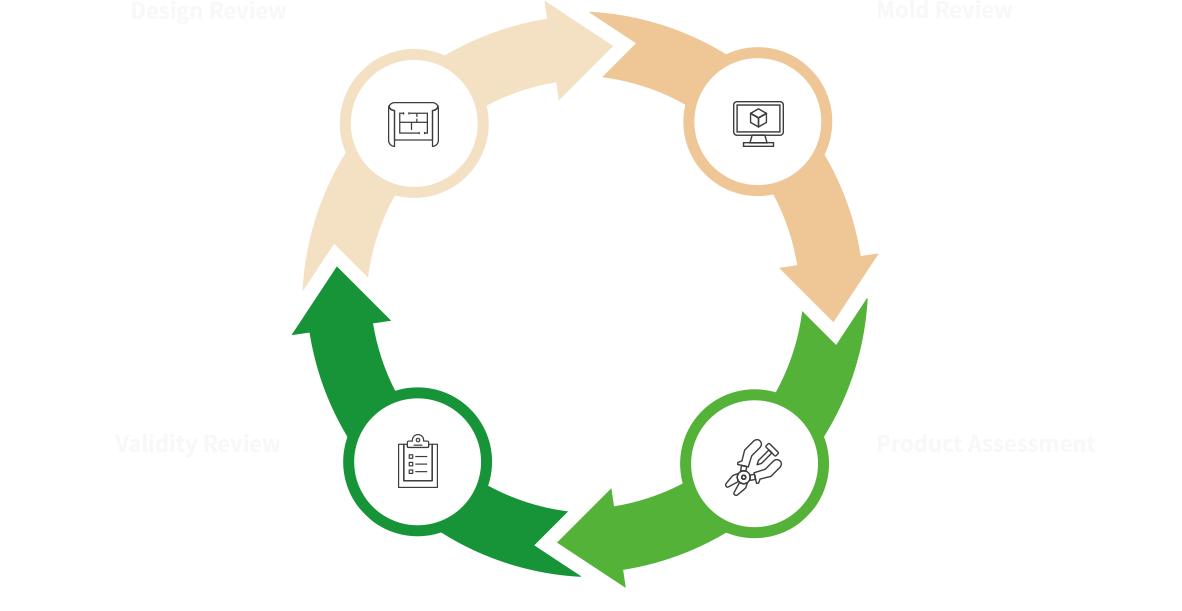
Quality Certifications
-
BIQS Certification
- SPPS Severity score: Below 6.75 points
- Filed Action (recall and campaign) “Zero”
- Manage to get Quality RRR below 6 within 6 months timeframe
- Keep improving/practicing BIQS certification continuously after getting 82% certified in 2019
-
SSQ Certification
- Manage and maintain the records of quality documents through computerization and establish efficient management system
- Select Q points and control
- Perform in-house audits and participate in trainings hosted by customers
- Perform audit on Tier 2 companies once a year (Nurturing Tier 2 companies)
-
SQ certification
- Randomly inspect to maintain minimum of SQ 600 points and perform a surprise inspection semiannually
- Establish annual quality nurturing plan for Tier companies(sub-contractors) and host workshops
- Keep nurturing auditors to train SQ-specialized personnel
- Strengthen the relationship with customers to comprehend their needs
-
IATF16949
- Continuously review to improve the necessary process required for quality management system
- Evaluate customer satisfaction on a regular basis and comprehend the problems
- Validate the procedures of each departments which are in documentation form and maintain the latest versions
- Record after comprehend/monitor the process and manufacture capabilities